Tip Ideas
We were discussing different variations of tips and came up with the following:
- An extending (antennae-like) tip
- Instead of a wire tip, make a plate for a larger heated area
- A curved or bendable tip to reach into crevices
- A hybrid scalpel/coagulating tip (a sharp edge to cut, but heated to coagulate)
- Use some sort of non-stick coating to get less char stuck to tip
Cautery Post Material
Got a response from Bovie about why they use brass posts instead of stainless steel:
“The brass was chosen because of its electrical resistance properties over stainless steel, even though stainless steel would be preferred over brass because of its corrosion properties and cosmetic cleaner look. The stainless steel has more resistance; this causes problems to the batteries and mold material (the ABS) around the post. I experimented with stainless steel before, preliminary testing of brass versus stainless steel indicated something like 10 times more resistance in the steel. With stainless steel posts, the batteries would drain much faster and the heat build-up could cause damage to the surrounding post material.”
So, it sounds like brass is a great option, especially if we are planning to make tips that will be used in this pen for now (so the ABS doesn’t melt). Extended battery life would be good in developing countries or areas with limited resources. The problem I see is that they might not be able to autoclave their stainless steel instruments with these tips because there might be electroplating.
Material Data Sheet from Bovie
[Material Data Sheet from Bovie Medical Corporation has been removed due to copyright restrictions.]
Talk with Dennis
by [SG]
I talked to Dennis today about making our prototype this weekend and any insight he has into the materials that we are going to use.
There are a few problems that we’ll have to look into:
- We can’t use brass for the wire at the tips because it will melt at the temperatures necessary for surgery. This is because the wire is much thinner than the posts, so since resistance is roughly inversely proportional to the cross section, the smaller the cross section the higher the resistance. Dennis recommended sticking with the material they use now, which is predominantly nichrome (the tips we found have an alloy of nichrome, iron, cr, al, etc.). Nichrome can withstand the heat of surgery and Dennis thinks that it can withstand autoclaving too.
- We also can’t use brass for the posts. This is because brass will corrode upon autoclaving. We can use stainless steel, but it is not a good conductor and thus may take a longer time to heat up the wire at the tip. Or, I was thinking that we could use a brass post but plate it with stainless steel. Dennis said that this wouldn’t work because the steel would separate upon plating because it is an alloy, and if we melt it to coat the brass, the brass would melt as well. Our option is to use chrome or nichrome plating, or make the posts out of chrome themselves. Plating the brass will be tricky, so we might have to “play” with a chemistry lab.
- Connecting the posts with the wire: This is tricky because we can’t solder the pieces, since the solder would melt at the temperatures necessary for cautery. Apparently, we have to weld the pieces, but we can’t use the one in the lab because that is too big and powerful. Dennis said we’d have to build our own mini-spot welder, which apparently isn’t too hard, actually “pretty simple with a transformer.” Or–I thought we could drill a tiny hole into the post and kind of cinch the wire inside/insert it in so that it would be tight enough. Dennis thought this might not be practical, because we’d need a 8/1000th drill, but he said we could get the necessary drill bit if we really thought this was the method to do it with. I guess another option is to get a hollow post, and cinch the wire inside, but we don’t know what making the post hollow will do. If we do make it hollow, perhaps using stainless steel isn’t a bad idea, because it would significantly reduce the time to heat up.
- White disc: Polypropylene is apparently fine, autoclavable, since it is a plastic solid. He said this was pretty cheap, all we would need was a cylinder of this stuff which we would slice for our prototype.
So I guess the next steps that we will need to do are:
- Mini-spot welder or cinching by hollow post or drilling hole?
Look into what making the post hollow would do.
- Stainless steel or nichrome post or nichrome plated over brass?
If we go by nichrome plated, we need to look into electroplating techniques.
Good news: We can get all materials we want in 24 hours, so we could definitely make our prototype this weekend.
Actually, Dennis has nichrome in the lab, but not medical grade, so we might want to order that. Polypropylene is in the lab as well, as is brass.
Call to Ailis and Response to Meeting with Dennis
by Sonya Makhni
Hmm, looks like we have some thinking to do…
I spoke to Ailis (briefly) and she like the idea of a retractable, antenna like tip. If we do end up using the same materials, maybe we could look in to the spring-loaded system we were talking about earlier…
Bovie Med Equipment is HERE!
Great news. The Bovie free samples are here!
What’s in the box:
-
2 AA01-S Cautery High Temp Fine Tip
These are two of use-and-throw pens. Sadly, they weren’t able to send me the reusable pens, probably because they are more expensive. But, these are good enough to test our tips on, and we can take one apart.
-
2 H101-S Replacement Tips
The one-use tips you would use on the reusable pens. We can’t test them on anything since we don’t have the pen that goes along with them, but we can see the morphology. An interesting thing I noticed: The tubes are actually slightly hollow, and the ends are actually cinched where the wire goes in! So it looks like the real company that makes these things uses the cinching method.
Properties of Materials
by [SG]
Hey guys, I found the specs on the materials we were looking for. Also, I’m trying to find a place that sells really tiny pieces of brass, but have not yet had much luck. I emailed a professor who has an electronics lab, though.
Polypropylene
melting point of polypropylene = 160 C
“Polypropylene (PP) is the material used for the autoclave bags and is suitable for steam autoclaving. However, it is not suitable for dry heat sterilization and this is why bags must be removed from the chamber as soon as the cycle finishes since the hot jacket walls produce a dry heat environment inside the chamber and the bag may melt if left inside overnight.”
- Maximum Temperature: 275°F 135°C
- Minimum Temperature: 32°F 0°C
- Autoclavable: Yes
ABS
melting point of ABS = 221°F = 105°C
- Maximum Temperature: 176°F 80°C
- Minimum Temperature: -4°F -20°C
- Autoclavable: No
- Melting Point: 221°F 105°C"
Brass
melting point brass = 900 C
autoclavable: yes
“Autoclave dissimilar metals (aluminum, brass, steel) in different loads as electroplating may occur which will permanently stain the tool.”
Group Chat with Dennis; Next Steps
by [SG]
A quick summary of what happened today:
Talk with Dennis:
We got a few things cleared up with the materials again. It turns out that
a) Brass does not corrode when autoclaved, at least not significantly. It will wear away with lots of use however.
b) Polypropylene is autoclavable too? According to our outside research. At this point we don’t know why an electrocautery tip can’t be autoclaved, since nichrome 80 (the wire material), the white disc, and posts are ALL autoclavable. We should find an autoclave and put one of our tips in there and see what happens.
Measurements:
- The brass posts are 0.062 inches with 17th/1000 in hole. The hole can be smaller, because the nichrome 80 wire diameter is 11/1000th inches.
What to do next:
- Focus on the retractable tip idea. Make them antenna-like or use braided wire and attach it to the end of the posts. This means that we need to track down brass tubing that is 0.062 inches in diameter, and polypropylene. Also, we need to find braided wire of that size (smaller than 17th/1000 in) to fit into the hollow. Maybe our prototype can even have plastic extendable regions, with a wire running through, if we cannot get these materials in time.
- Find an autoclave, and put our tips in and see what happens. We tried calling Bovie again, and it seems like someone from the engineering department should be e-mailing us about this. Hopefully, this will clear up whether the tips cannot physically be autoclavable or if it’s a regulatory/company issue.
- Find out from the chem lab if we can chrome-coat brass using electroplating, so that the posts will be longer lasting.
First Priority: finding the braided wire, brass tubing.
Final Design Plan
by [SG]
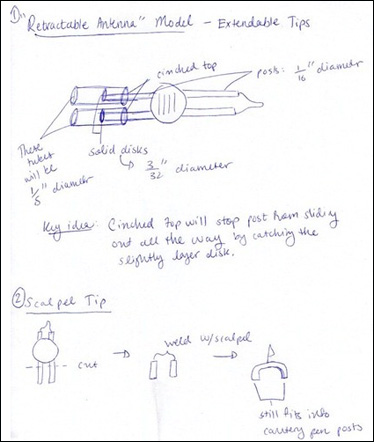
Final design plans for the “retractable antenna” model and the scalpel tip
The final design plan for the project will be to make two different varieties of tips: a retractable antenna model that will allow the tips to be extended to the desired 5" during surgery, and the scalpel tip model that will have a scalpel tip on the end instead of the current wire.
Also:
- Ordered multiple brass tubing today, of sizes 1/16", 3/32", 1/8", and 5/32" to build the retractable antenna model.
- Will get the scalpels from Ailis.
Dennis Meeting
We met with Dennis to see if our design would be feasible. He said we could try making some things tomorrow. He will be in D-lab starting at 10:30 am, so as soon as we get the materials, we should head over.
As for the retractable antenna model, he said if this were to be used in a medical setting, the junction between the larger and smaller rods would have to be sealed really well so that tissue and other contamination does not get in or can be cleaned out easily if it does.
He also said that we might have trouble with the plug into the pen if we use the larger tubes at the junction. We tried to buy solid brass rods so that we could drill a hole in them, but it would have been $30 to ship them in time. We are instead going to check out Economy Hardware and see if they have anything. If not, we will try to fill in the extra space with solder or something else.
The third thing we talked about was the design of the scalpel tip. We thought about changing the design from one where the scalpel itself heats up to one where it’s a combination of a scalpel and a wire that heats up. The issue with both is that the scalpel will get in the way when the user wants to cauterize. We therefore need to think of a design that will avoid this interference. [SG] and I started thinking of a design that would have 2 retractable tips so that if the scalpel is out, the cauterizing wire is in, if the cauterizing wire is out, the scalpel is in. We need to think about this more though.