Your mission: Clean up planet earth and re-establish plant life.
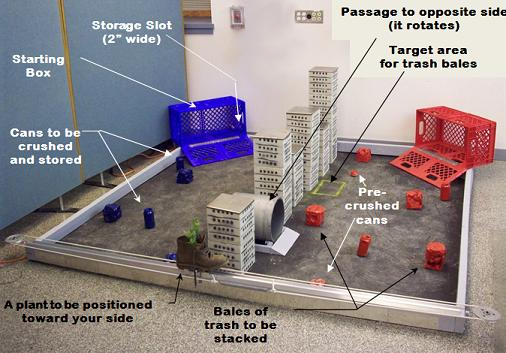
The challenge for this year’s 2.007 robots is to clean up the environment. (Image by Dan Frey.)
Robots begin inside their respective starting box (12" high, 22" wide, 10" deep) with the door closed. Once time starts, the door opens forming a ramp. You will have 60 seconds to exit the box, clean up the table, and/or retrieve the plant. For the first 10 seconds, your robot operates autonomously and in the subsequent 50 seconds under radio control.
The fate of the planet is in your hands!
Parts and Equipment
Project Kit List (PDF)
SolidWorks Parts Archive (ZIP) (This ZIP file contains: 36 .sldprt files, 1 .rpt file, 1 .xlo file, 1 .igs file and 1 .sldasm file.)
Notes on Lithium Polymer Batteries (PDF)
Milestones
WEEK # | LAB ACTIVITIES | MILESTONES |
---|---|---|
1 | Explore kit & contest (PDF) | Kit and contest exploration (PDF) |
2 | Build a simple car & preliminary strategy (PDF) | Develop strategy and work toward final car design (PDF) |
3 | Design concept (PDF) | Develop concept and finalize car design (PDF) |
4 | Design of most critical module (PDF) | Design MCM and build final car (PDF) |
5 | Fabrication of most critical module (PDF) | Fabricate MCM (PDF) |
6 | Complete MCM fabrication (PDF) | |
7 | Demonstration of most critical module (PDF) | Demonstration of MCM (PDF) |
8 | Integration of design (PDF) | Completion plan (PDF) |
9 | Demonstration of integrated machine (PDF) | |
10 | Design iteration (PDF) | |
11 | Fabrication of improved machine (PDF) | |
12 | Demonstration of improved machine | |
13 | Final refinements | |
14 | Debriefs with section (PDF) |
Past Projects
The 2.007 theme changes every year to provide an ongoing challenge for students and robots.
2003 Project: The Two Tables
2005 Project: Tic Tech Toe
-
Contest Video: The 2005 contest Tic Tech Toe contest was videotaped over two nights, Ses #24 and the next day.
First Round (MP4 - 395MB)
Finals (MP4 - 638MB)