« Previous: Assignment 2: “Hello World” Fabric PCBs, Part 1 | Next: Assignment 4: Yarn » |
For this assignment you will work in teams to create an artifact that includes a fabric PCB. The artifact should include an ATtiny13 microcontroller, at least two outputs and at least one digital (switch) input. A picture of the circuit that I made is below. You can use this circuit as a starting point, but you should not just turn in an identical copy. You should modify my circuit in some way and/or incorporate it into a larger project by, for example, sewing it into a garment.
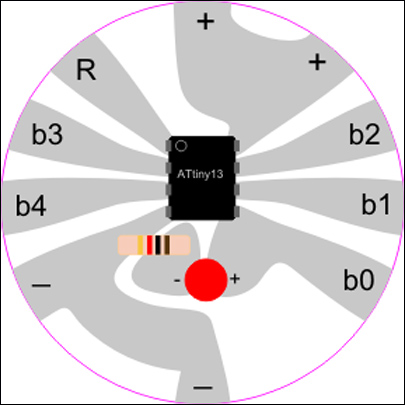
An example fabric PCB circuit.
With your team you should create a webpage that documents your project. Your page should include pictures, including at least one close up of your PCB and one image that shows the entire project, and a paragraph about your experience. Also create a short video of your project in action; post the video online (Vimeo, YouTube, or your own site) and include a link to your video in your documentation page.
Sample Student Work
These samples are presented courtesy of the students and used with permission.