« Previous: Return to Assignment 7 description | Next: student work sample » |
By Nadia Cheng
Developing functioning tunable-stiffness materials made of a passive scaffold + an active material.
Motivation
My research has been focused on developing novel tunable stiffness materials for soft robotics applications. Tunable stiffness materials would allow a robot to transition between passive, morphable states and rigid, loading-bearing ones. Most recently, I have been focused on developing composites made of a passive scaffold (like a flexible, open-cell foam, which is capable of “shape memory”) coated in an active material, whose materials properties can be changed. Specifically, I have been investigating foams (both commercial and 3D-printed ones) coated with wax, which can be thermally activated to transition between solid and liquid states.
The images below show some of the work I have been doing in this area.
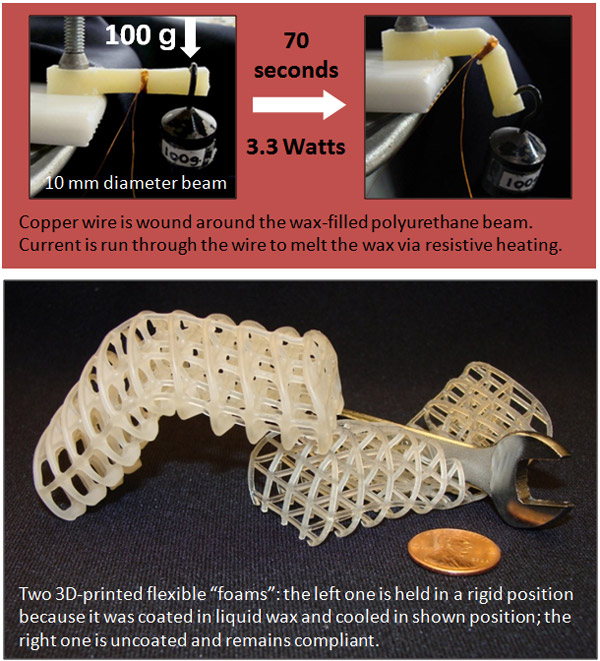
Recent work in tunable stiffness structures.
Project Proposal
My past work has involved working with commercial and 3D-printed foams only; therefore, I have been limited in how the heating elements for melting the wax are integrated. Ideally, I would like to have the heating elements integrated into the passive scaffold material. For the nonwoven class assignment, I explored molding silicone as a manufacturing method that allows me to directly mold heating elements into the silicone struts. The images below are from the nonwoven assignment.
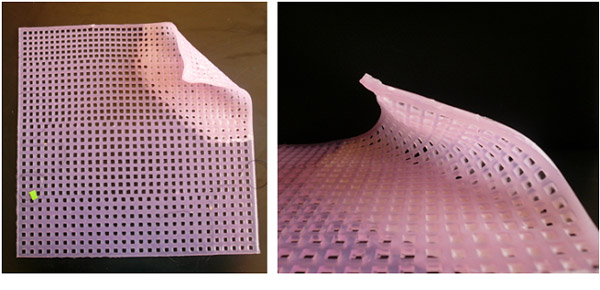
Examples of a cast silicone grid, from work on the Nonwoven assignment.
For this project, I would like to explore various scaffold materials, including silicone and steel yarn, which heats up via resistive heating. Not only can steel yarn serve as the heating elements, but it can serve as the passive scaffold itself (for instance, if I crochet it into a scaffold-like pattern). I also want to use various types of heating elements in addition to the steel yarn. Specifically, I want to use both line sources and point sources of heating. Finally, the main goal of my final project is developing functioning demonstrations of thermally activated tunable stiffness composites, but in 2D and 3D forms.
Timeline
- Week 1: Construct 2D folding silicone grid with embedded line heating sources
- Week 2: Construct 2D folding knitted/crocheted steel yarn grid with line heating sources
- Week 3: (I will be out of town for a conference, so I will have to do this week’s task before or after this time period) Construct 3D silicone grid with line heating sources
- Week 4: Tie up loose ends (figuratively and maybe literally), final presentation!
« Previous: Return to Assignment 7 description | Next: student work sample » |